Hunkeler Innovation Days 2023 – Automatiser plus et mieux
Cet article est paru dans Acteurs de la Filière Graphique n°141 (mars 2023)
Avec 6700 visiteurs massés dans un espace relativement contraint, l’édition 2023 des Hunkeler Innovation Days confirme le succès grandissant d’un événement qui fêtait ses dix ans en 2022. L’UNIIC y embarquait – comme en 2019 – une délégation d’une trentaine d’imprimeurs pour s’enquérir sur place (au Centre d’Exposition de Lucerne, en Suisse) des avancées matérielles et logicielles qui s’opèrent dans l’univers des lignes de production numériques. Avec toujours ce même mot d’ordre : automatiser plus et mieux.
« La vision d’Hunkeler est simple : c’est celle d’une industrie totalement automatisée.»
Mickaël Hiblot (Directeur des ventes Hunkeler)
L’événement porte indéniablement quelque chose d’atypique dans la mesure où, de façon transparente et jusque dans son intitulé, il est porté par un fournisseur de matériel intercalé en amont et en aval du travail d’impression, l’offre ‘brandée’ Hunkeler allant en effet des débobineurs de papier en entrée de ligne, jusqu’aux outils de finition en bout de ligne. Un organisateur/fournisseur qui choisit donc de s’entourer de partenaires, mais aussi de simili-concurrents (Duplo, Müller Martini, Horizon etc.), pour construire un salon de solutions et modules aussi complémentaires que possible, sur des marchés, produits et services variés : catalogue, brochure, transpromo, éditique, livre, notice, routage etc. Pari gagné : ce rendez-vous s’est imposé comme l’un des plus engageants dans le paysage événementiel des Industries Graphiques, en une petite décennie. « La vision d’Hunkeler est simple : c’est celle d’une industrie totalement automatisée » nous explique Mickaël Hiblot, son Directeur des ventes. En l’occurrence, personne ne saurait s’extraire d’un mouvement d’automatisation global qui donnera immanquablement à s’observer à la Drupa 2024 (une édition très attendue, huit ans après la précédente au format « physique »), au-delà des seuls segments relatifs à l’impression numérique. Pour autant, c’est bien l’impression numérique qui donne le « La » d’un mouvement qui se précise. Les visiteurs, venus nombreux, ne s’y sont pas trompés…
Une automatisation de plus en plus flexible et permissive
L’automatisation des lignes de production n’apparaît comme une performance louable qu’à la condition de satisfaire à des exigences de variabilité et de flexibilité de plus en plus claires. C’est d’ailleurs dans ce rapport précis automatisation/variabilité que vient se nicher l’essentiel des innovations observées cette année, alors que les discours n’ont pas changé d’un iota. Ne pas arrêter les machines, prévenir les défauts de qualité, éviter les pannes par anticipation et intégrer les opérations de maintenance à la logique de lignes de production ultra-optimisées, tel est le credo martelé par une majorité de fournisseurs depuis l’édition précédente (à minima), tout en promettant des runs avec des changements de contenus, formats, paginations, découpes et pliages à la volée. Tant en impression qu’en finition. Des promesses qui ont pris corps au gré de démonstrations convaincantes tenues sur place, avec de belles nouveautés à la clé : « Chez Laballery, on essaie d’organiser la production en fonction du papier sur lequel nous imprimons. Avec certaines des machines que j’ai vues ici [cf. le module Hunkeler Media changer RX8, NDLR], on peut s’imaginer jongler d’une bobine à l’autre pour passer d’un média à un autre sans arrêter sa ligne de production, gérer en temps réel les demandes de réassorts avec les besoins en papier associés, du collage à la volée jusqu’à la parfaite intégration de la tension des bandes… Les possibilités que ça ouvre sont passionnantes » s’enthousiasme notamment Hubert Pédurand, de passage sur le stand Hunkeler, face à des double-débobineurs qui, demain, « pourraient être triple ou quadruple », nous assure-t-il. Confirmant que les machines offset pourraient elles aussi basculer sur ce type d’équipements en pré/post presse, Mickaël Hiblot tient par ailleurs à souligner que « Hunkeler travaille en open source. Nous voulons pouvoir rendre nos matériels compatibles avec ceux de nos partenaires », indiquant simplement s’assurer de « la validité des systèmes en amont ». Une philosophie qui éclaire jusqu’à l’existence de ce salon, où l’innovation est partagée et irrigue par petites touches l’ensemble des stands, l’objectif étant bien celui-là : construire des lignes de production à sa guise, comme dans un jeu de lego, sans se retrouver bridé par des pièces refusant de s’imbriquer.
« Le salon s’attache à proposer des solutions compatibles et optimisées pour des lignes de production calées à 200 mètres/minute, finition incluse.»
Trop d’automatisation tue-t-il l’expertise de l’imprimeur ?
Au registre des opérations automatisables, sur des lignes de production modulables à souhait – ou presque – on se perd rapidement à énumérer les services proposés par les fournisseurs. Il ne faudrait à ce titre pas oublier combien la dimension software est nourrie par la même obsession, les logiciels de commande, pilotage et de maintenance étant pensés comme le point de départ d’une philosophie unique, visant à tout relier : du traitement prépresse aux dernières opérations de finition. « Notre workflow dynamique de nouvelle génération FreeFlow dispose de capacités prédictives. C’est-à-dire qu’il est capable d’apprendre et de s’adapter. Correctement configuré, il peut même travailler seul, comme un opérateur » assène notamment Hubert Soviche (Xerox). Ainsi en va-t-il également des opérations d’ennoblissement ou d’assistance technique, ce dernier point étant assuré pour le cas de Xerox par « la solution de réalité augmentée CareAR qui, plutôt que de demander à l’opérateur de nous décrire son problème, va lui demander de nous le montrer » résume Isabelle Savin, cheffe de produits et support ventes. Sans collecter de data, nous dit-on, une Intelligence Artificielle (IA) s’attache en effet à analyser des images pour poser des diagnostiques à distance, proposant des aides en forme d’annotations dynamiques et disposant même de ralentis pour identifier précisément les manœuvres potentiellement problématiques. Une logique englobante qui dessine les contours de ce que d’aucuns continuent d’appeler l’industrie 4.0, soit des modèles de production de plus en plus automatisés par interfaces numériques interposées, avec même une touche d’IA pour devancer et minimiser les interventions humaines. Si le discours est bien rôdé et les démonstrations huilées, sûrement faut-il objecter que cette évolution dopée aux algorithmes et aux IA, dont l’intégration ira grandissante, ne doit pas avoir pour effet d’opacifier de trop une mécanique hardware qui doit rester aux mains de l’exploitant industriel. Nous l’écrivions dans une tribune publiée en ces pages voilà bientôt trois ans (cf. Acteurs Graphiques n°131) et nous le redisons volontiers : « De la même façon qu’il serait faux de penser que le prépresse a disparu en impression numérique en même temps que la forme imprimante, sous-entendre que la technicité de l’impression serait dépassée, absorbée par des machines n’exigeant soi-disant plus que de savoir manipuler des potards, c’est prendre le risque de voir disparaître des savoir-faire pourtant précieux ». En l’occurrence, ceux de l’imprimeur.
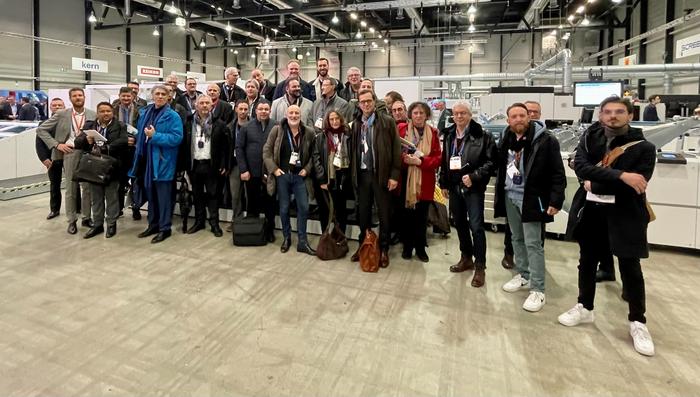
Une délégation UNIIC était du voyage en Suisse, à Lucerne, pour cette nouvelle édition des Hunkeler Innovation Days.
Qualité contrôlée : « Là n’est plus le débat »
« Nous allons encore trois à quatre fois moins vite en finition qu’en impression » nous disait Steve Levy (Ricoh) en 2019, lors de la précédente édition des Hunkeler Innovation Days. Or, quatre ans plus tard, ce différentiel n’existe encore qu’à la marge et sauf à investir dans des presses qui roulent à 400 mètres/minute (auquel cas il faudra effectivement doubler les lignes de finition pour continuer à imprimer à pleine vitesse), le salon s’attache à proposer des solutions compatibles et optimisées pour des lignes de production calées à 200 mètres/minute. La vitesse ne faisant toutefois pas tout, il est un quasi-consensus que nombre de fabricants ont tenu à mettre en avant : « sur le type de machines que nous exposons ici, la qualité n’est plus un débat » avance notamment Verena Hahn (Canon), au sujet notamment de sa gamme Varioprint. Une assurance que l’on retrouve quasiment trait pour trait chez les autres fabricants de systèmes d’impression, y compris d’ailleurs en dehors des supposées grosses écuries que sont HP, Kodak, Xerox ou Ricoh. « La qualité dépend chez nous de la vitesse d’impression, sachant que sur notre Truepress Jet520HD, nous pouvons aller jusqu’à 150 mètres/minute. Mais nous pouvons imprimer sur tout type de papier, avec une qualité quasi-égale à l’offset » confirme Thomas Lossec (Screen Europe). Si le débat n’est donc plus là, il ne s’est pas déporté très loin… « La qualité est là, mais il faut la contrôler souvent. Le problème que nous avons tous, c’est l’assèchement des têtes d’impression. C’est pourquoi nos machines VPX s’attachent à contrôler la qualité d’impression de manière automatisée toutes les quatre feuilles » précise Verena Hahn pour Canon. Chez Kodak, autre approche : « la Prosper Ultra 520 s’appuie sur un taux d’encrage très dense. Ce sont des encres aqueuses de fabrication Kodak qui comptent environ 70 composants, dont… des antibiotiques ! Pourquoi ? Parce qu’ils permettent de nettoyer les têtes d’impression directement à l’usage » détaille Laurent Mathieu (Directeur des ventes Benelux). Si chacun s’emploie assez naturellement à défendre le caractère écoresponsable d’encres composées à base d’eau (quoiqu’il faudrait bien sûr s’intéresser de près à l’ensemble des composants pour tirer telle conclusion), certains assurant même qu’elles se sont avérées tout à fait désencrables (condition sine qua non pour entrer dans la boucle de valorisation Citeo et ne pas attribuer de malus aux metteurs sur le marché), la question que pose une densité accrue en termes d’encrage – Kodak revendique « 40 milliards de gouttes à la seconde » – est naturellement d’ordre économique : l’impression numérique est-elle toujours victime du coût de ses consommables, et notamment des encres ? La question se pose, à plus forte raison si les exigences de qualité inclinent à en augmenter le volume de consommation…
« Sur le type de machines que nous exposons ici, la qualité n’est plus un débat. » Verena Hahn (Canon)
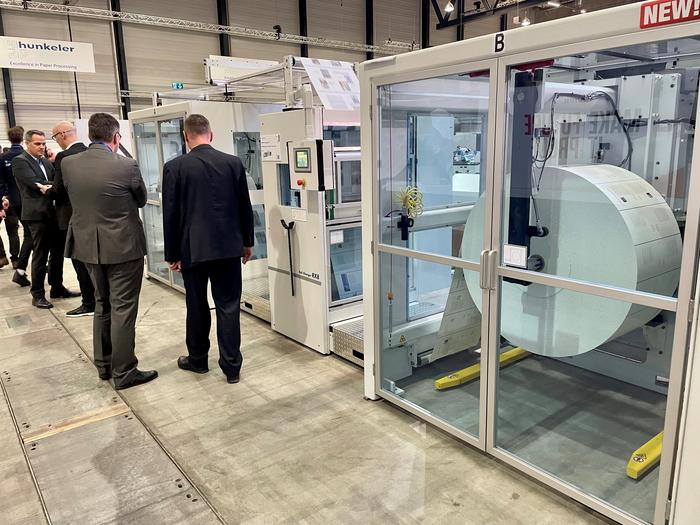
Les lignes modulaires Hunkeler Starbook ont fait forte impression cette année, autorisant notamment en entrée de ligne changements de bobines à la volée, puis des opérations de production (format, découpe, pliage, collage etc.) variables en « book-to-one » et enfin un traitement logistique automatisé, pour trier jusqu’à 2000 blocs de livres par heure dans différents conteneurs de transport.
Coût des consommables : éternels freins à l’investissement ?
Face à pareilles critiques, les réponses sont peu ou prou les mêmes depuis une douzaine d’années : si les encres sont « chères », c’est parce qu’elles intègrent effectivement des coûts de recherche & développement importants sur ces technologies. Et leur coût n’est soutenable qu’à la condition d’adopter un positionnement stratégique adapté, tout en valorisant sur le plan industriel et organisationnel les gains (de temps, notamment) obtenus par ailleurs : « plus de RIP pour le CTP, fini les plaques aluminium, terminée la chimie, le séquencement de production – je plaque, j’imprime par cahiers, j’attends que ça sèche, je plis mes cahiers, j’assemble mes cahiers, je broche mon livre – est divisé par cinq en durée etc. Au final un livre qui mettait cinq jours à se produire en offset chez Laballery se traite en cinq heures, avec deux fois moins de personnel » témoigne Hubert Pédurand, qui dit toutefois attendre « une hausse globale de la production en jet d’encre pour voir le prix des encres baisser ». Car oui, le sentiment général est malgré tout bien celui-là : les consommables sont encore chers en impression numérique quadri, au regard d’une demande insuffisamment volumique pour s’autoriser toute forme de légèreté, quand il s’agit d’investir dans ce type de matériel. Or, parmi les failles d’un modèle économique inclinant à minimiser les coûts, au regard des dépenses nécessaires pour se fournir en consommables et donc nourrir ses machines, il y a la tentation de réduire sa main d’œuvre. Au premier chef, déjà, parce que c’est ce vers quoi pousse l’automatisation des systèmes de production. « Nos machines sont conçues pour que l’opérateur ait moins de tâches à effectuer que jamais, tout en se déplaçant le moins possible dans l’atelier. Notre volonté est d’automatiser un maximum de réglages, notamment pour les changements de formats » illustre Marc Giustiniani, Directeur commercial France chez BlueCrest, pendant la démo d’une machine de mise sous pli (modèle Epic). S’il ne s’agit encore là que de faciliter le travail des opérateurs, tout le monde en convient : cela aura forcément des effets sur l’emploi. « Le conducteur de demain dirigera des lots de machines » s’avance même à affirmer Mickaël Hiblot, sous-entendant sans faire de mystères que là où il fallait deux à trois techniciens par atelier, il n’en faudra bientôt plus qu’un. Au risque de s’appauvrir humainement ? « L’enjeu, ce sera d’affecter de l’emploi à des tâches à la fois moins pénibles et plus valorisantes, voire à songer à de nouvelles fonctions. Dans ce domaine-là aussi, il faudra innover » poursuit-il. De manière concomitante, il faudra nécessairement penser à construire et organiser le transfert de compétences, de sorte à rendre possible le basculement technologique pour des équipes souvent habituées à travailler sur des outils d’impression/finition d’une tout autre nature. Un défi collectif que ces Hunkeler Innovation Days ont mis en avant de façon concrète, sans même le dire explicitement. Et nul doute que dans un peu plus d’un an maintenant, la Drupa enverra un message semblable…